Explore how computer vision in battery manufacturing enables real-time defect detection, robotic assembly, label verification, and safer, high-quality production.
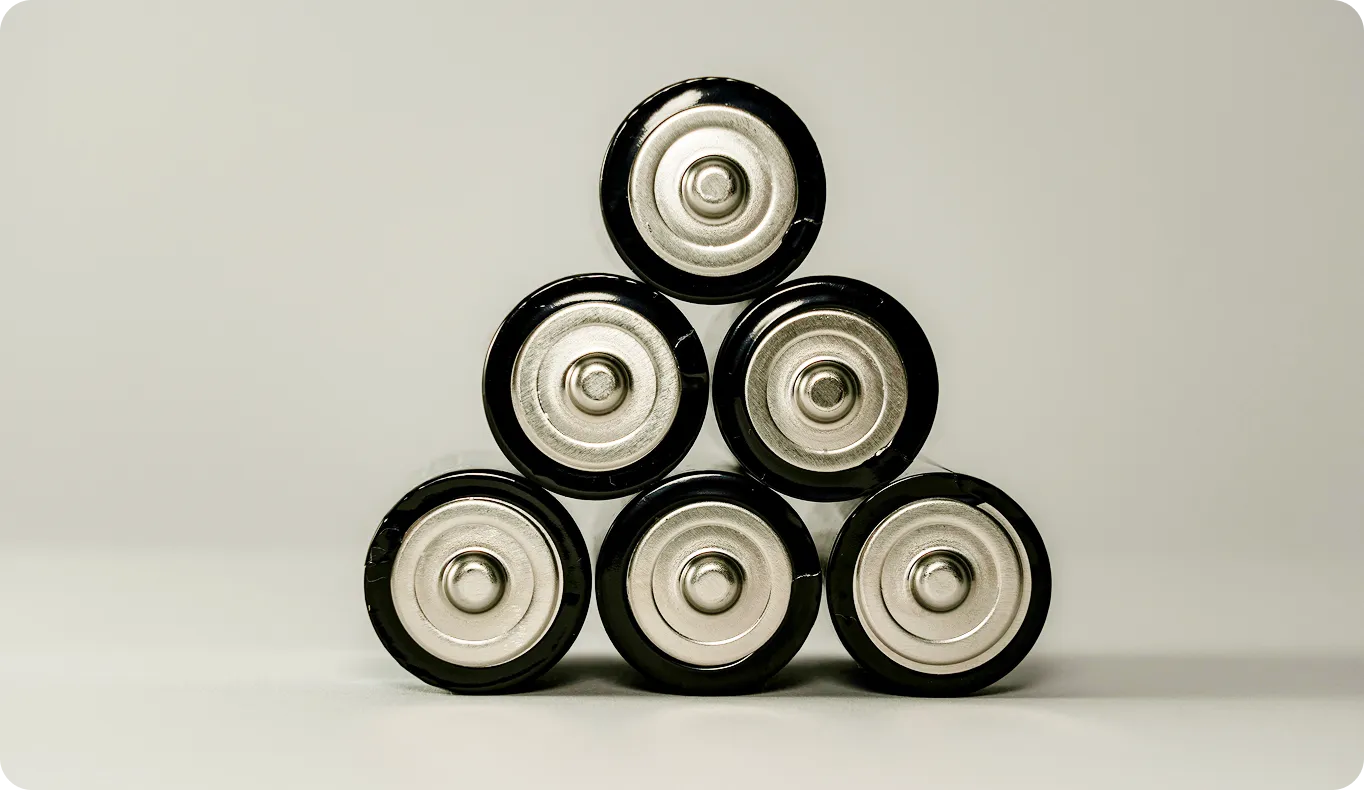
Explore how computer vision in battery manufacturing enables real-time defect detection, robotic assembly, label verification, and safer, high-quality production.
Batteries are an important part of our daily lives. They keep phones charged, laptops running, and electric vehicles moving. We rely on them more than we realize, yet we rarely stop to think about how they’re made. In reality, the process of making batteries is far more complex than most people might think.
Battery manufacturing processes depend on multiple carefully coordinated steps, from material preparation to final inspection. Even a small mistake, like a misaligned layer or a loose component, can impact performance or lead to safety issues.
For years, manufacturers have relied on manual inspections and basic sensors to identify issues. However, as production has expanded and quality expectations have grown, these traditional methods are struggling to keep up.
That’s why many manufacturers are now turning to computer vision, a branch of AI that enables machines to interpret and understand visual information. Specifically, in battery manufacturing, it’s being used to detect defects, measure components with precision, and monitor each step of the process in real time.
In this article, we’ll explore how batteries are made and how computer vision is transforming the battery manufacturing process to improve quality, increase efficiency, and support the future of energy technology. Let’s get started!
Battery production is a careful step-by-step process that needs to be extremely precise. It starts with coating special materials onto thin metal sheets, which are then cut and stacked together with other layers to form the battery’s core.
After that, liquid electrolyte is added, the battery is sealed, and it goes through charging and testing to make sure it works properly. Finally, it’s labeled and packaged, ready to power everything from phones to electric cars.
Since batteries are so sensitive, tiny flaws can cause big problems. A defect as small as a hairline scratch or a slight misalignment can reduce battery life, compromise safety, or lead to battery failure. With more devices and vehicles running on batteries, manufacturers are looking for innovative and faster ways to ensure each unit is built without faults.
This is where computer vision comes into play. Computer vision models like Ultralytics YOLO11 that support various tasks like object detection and instance segmentation can be trained to recognize battery components, detect surface defects, and monitor the accuracy of assembly in real time.
By analyzing images from high-resolution cameras, these models help double-check that every part is correctly placed and free from defects. This enables faster and more consistent battery production with fewer errors.
Here’s a closer look at some of the key computer vision tasks that can support and streamline the battery manufacturing process:
Now that we have a better understanding of the core computer vision tasks used in battery manufacturing, let’s walk through how these tasks can be applied across different stages of production to enhance quality, safety, and efficiency.
Electrode coating is a crucial part of the battery production process. In this step, a thin layer of active material is applied to metal foil to form the battery’s electrodes.
Small defects, such as bubbles, pinholes, or uneven edges, can occur during coating. While they may seem minor, these flaws can lead to overheating, poor performance, or reduced battery life. They’re also difficult to detect with the naked eye, especially in high-volume manufacturing environments.
Computer vision models can support quality control by analyzing high-resolution images to detect and flag surface defects in real time. Techniques like instance segmentation allow the system to identify different regions of the electrode and highlight irregularities, making the inspection process more accurate and consistent than manual checks.
An interesting example of this is a system developed by researchers that combines X-ray computed tomography (CT) with computer vision to inspect lithium-ion battery electrodes. It uses 3D scans to detect internal defects such as cracks and flaws.
Once electrodes are coated successfully, they have to be assembled into the battery’s internal structure using either winding or stacking. Winding rolls the electrode and separator sheets into a spiral shape, while stacking places the layers flat on top of each other.
Both techniques require precise alignment, often down to just a few microns. A slight shift can affect how electricity flows through the battery, leading to lower performance or a shorter lifespan.
To achieve this level of accuracy, manufacturers are using computer vision to guide robotic arms during assembly. High-resolution cameras and 3D sensors help position each layer correctly and spot issues like dust, bending, or warping.
These systems make it possible to keep spacing, tension, and alignment consistent, which improves both quality and production speed. In some cases, robots also use force sensors along with visual data to gently handle sensitive materials.
During battery cell assembly and packaging, components such as tabs and casings are joined through welding or sealing. These joints are vital for maintaining electrical flow and structural safety.
The smallest crack or weak point can cause short circuits, overheating, or, in extreme cases, thermal runaway (a dangerous chain reaction where the battery overheats uncontrollably and may catch fire or explode).
Manufacturers are adopting computer vision solutions paired with thermal imaging to improve this step. These systems can scan each weld in real time, checking for defects such as cracks, gaps, or weak spots.
While visual inspection can catch surface-level issues, some defects are hidden beneath the surface or cause uneven heat distribution, which standard cameras or the human eye can’t detect. Thermal imaging can reveal these hidden issues by showing how heat spreads through the weld, making it easier to identify weak joints or incomplete connections that could lead to failures later on.
Battery manufacturing involves a precise process of cutting, stacking, welding, and sealing. Every step is carefully timed and automated. But even in controlled environments, small foreign objects can slip through. A loose screw or metal shard left inside a battery pack can cause short circuits, internal damage, or fires.
To solve this, manufacturers are relying on computer vision systems built specifically for foreign object detection. These systems use high-resolution cameras and 3D vision to scan trays and modules before final sealing. They are trained to detect unwanted objects and respond immediately, by stopping the line, alerting a technician, or rejecting the affected pack, without interrupting production flow.
For instance, in EV (electric vehicle) battery assembly, computer vision is used to inspect trays for foreign objects just before final sealing. These systems can detect misplaced tools, loose screws, or debris that manual inspections might miss. By identifying these issues early, they help prevent electrical failures, avoid production delays, and reduce safety risks.
Once a battery pack is fully assembled, the last step is inspecting the packaging and labels. A damaged seal, dented casing, or misprinted label can cause problems down the line. These issues may affect product safety, delay shipments, or lead to regulatory failures if left unchecked.
Manual inspection at this stage can be slow and unreliable, especially with large volumes, whereas computer vision systems can perform the same checks quickly, consistently, and with greater accuracy.
For example, let's say a battery pack has a typo on its label. Object detection can first identify the part of the label that contains text, and then OCR (optical character recognition) technology can be used to read and verify the content. If there's a typo or formatting error, the system can flag the pack for correction before it moves further down the line.
Here’s a quick glimpse at the ways in which computer vision improves battery manufacturing:
While computer vision brings various advantages to the table, there are a few limitations to consider when adopting these systems. Here are some factors to keep in mind:
Computer vision is steadily changing battery manufacturing. It can be used to detect small defects, guide robotic arms with precision, inspect welds and seals, and verify final packaging.
Each step can be monitored closely by Vision AI to make sure every battery meets high safety and quality standards. These systems are faster and more consistent than manual checks, helping manufacturers reduce waste and avoid costly errors. As technology continues to evolve, it's likely that computer vision’s role in battery production will grow.
Join our community and explore our GitHub repository to discover more about AI. If you're looking to start your own Vision AI project, check out our licensing options to get started. You can also see how AI in healthcare and Vision AI in retail are making an impact by visiting our solutions pages.