Découvrez comment la vision par ordinateur dans la fabrication de batteries permet la détection des défauts en temps réel, l'assemblage robotisé, la vérification des étiquettes et une production plus sûre et de meilleure qualité.
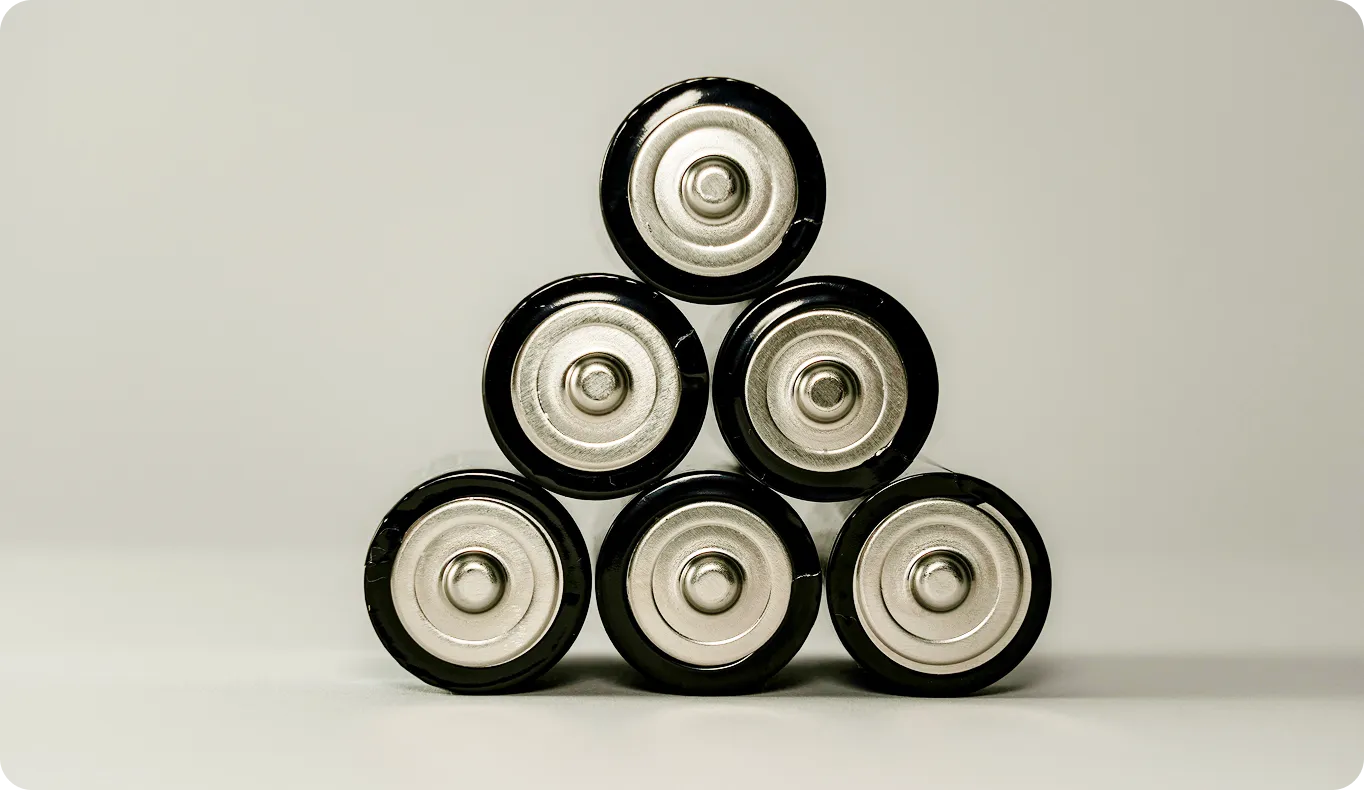
Découvrez comment la vision par ordinateur dans la fabrication de batteries permet la détection des défauts en temps réel, l'assemblage robotisé, la vérification des étiquettes et une production plus sûre et de meilleure qualité.
Les batteries sont un élément important de notre vie quotidienne. Elles permettent de charger les téléphones, de faire fonctionner les ordinateurs portables et de faire avancer les véhicules électriques. Nous dépendons d'elles plus que nous ne le pensons, mais nous nous arrêtons rarement pour réfléchir à la manière dont elles sont fabriquées. En réalité, le processus de fabrication des piles est bien plus complexe que la plupart des gens ne le pensent.
Les processus de fabrication des batteries dépendent de plusieurs étapes soigneusement coordonnées, de la préparation des matériaux à l'inspection finale. Même une petite erreur, comme une couche mal alignée ou un composant mal fixé, peut avoir un impact sur les performances ou entraîner des problèmes de sécurité.
Pendant des années, les fabricants se sont appuyés sur des inspections manuelles et des capteurs de base pour identifier les problèmes. Cependant, avec l'augmentation de la production et des attentes en matière de qualité, ces méthodes traditionnelles ont du mal à suivre.
C'est pourquoi de nombreux fabricants se tournent désormais vers la vision par ordinateur, une branche de l'intelligence artificielle qui permet aux machines d'interpréter et de comprendre les informations visuelles. Dans le domaine de la fabrication de batteries, elle est notamment utilisée pour détecter les défauts, mesurer les composants avec précision et contrôler chaque étape du processus en temps réel.
Dans cet article, nous allons étudier la fabrication des batteries et la manière dont la vision par ordinateur transforme le processus de fabrication des batteries afin d'améliorer la qualité, d'accroître l'efficacité et de soutenir l'avenir de la technologie énergétique. Commençons par le commencement !
Voici un examen plus approfondi de quelques-unes des tâches clés de vision par ordinateur qui peuvent soutenir et rationaliser le processus de fabrication des batteries :
Maintenant que nous avons une meilleure compréhension des principales tâches de vision par ordinateur utilisées dans la fabrication des piles, voyons comment ces tâches peuvent être appliquées à différents stades de la production pour améliorer la qualité, la sécurité et l'efficacité.
Le revêtement des électrodes est une étape cruciale du processus de production des batteries. Au cours de cette étape, une fine couche de matériau actif est appliquée sur une feuille métallique pour former les électrodes de la batterie.
De petits défauts, tels que des bulles, des trous d'épingle ou des bords irréguliers, peuvent survenir pendant le revêtement. Bien qu'ils puissent sembler mineurs, ces défauts peuvent entraîner une surchauffe, de mauvaises performances ou une réduction de la durée de vie de la batterie. Ils sont également difficiles à détecter à l'œil nu, en particulier dans les environnements de fabrication en grande série.
Les modèles de vision par ordinateur peuvent contribuer au contrôle de la qualité en analysant des images à haute résolution pour détecter et signaler les défauts de surface en temps réel. Des techniques telles que la segmentation des instances permettent au système d'identifier différentes régions de l'électrode et de mettre en évidence les irrégularités, ce qui rend le processus d'inspection plus précis et plus cohérent que les contrôles manuels.
Un exemple intéressant est celui d'un système mis au point par des chercheurs qui combine la tomographie assistée par ordinateur à rayons X et la vision par ordinateur pour inspecter les électrodes des batteries au lithium-ion. Il utilise des scans en 3D pour détecter les défauts internes tels que les fissures et les imperfections.
Une fois que les électrodes ont été enduites avec succès, elles doivent être assemblées dans la structure interne de la batterie par enroulement ou empilage. L'enroulement consiste à enrouler les feuilles d'électrodes et de séparateurs en forme de spirale, tandis que l'empilage consiste à placer les couches à plat les unes sur les autres.
Ces deux techniques exigent un alignement précis, souvent à quelques microns près. Un léger décalage peut affecter la manière dont l'électricité circule dans la batterie, entraînant une baisse des performances ou une réduction de la durée de vie.
Pour atteindre ce niveau de précision, les fabricants utilisent la vision par ordinateur pour guider les bras robotisés pendant l'assemblage. Des caméras à haute résolution et des capteurs 3D permettent de positionner correctement chaque couche et de repérer les problèmes tels que la poussière, les courbures ou les déformations.
Ces systèmes permettent de maintenir l'espacement, la tension et l'alignement cohérents, ce qui améliore à la fois la qualité et la vitesse de production. Dans certains cas, les robots utilisent également des capteurs de force et des données visuelles pour manipuler en douceur les matériaux sensibles.
Lors de l'assemblage et de l'emballage des éléments de batterie, les composants tels que les languettes et les boîtiers sont assemblés par soudage ou scellement. Ces joints sont essentiels pour maintenir le flux électrique et la sécurité structurelle.
La moindre fissure ou le moindre point faible peut provoquer des courts-circuits, une surchauffe ou, dans les cas extrêmes, un emballement thermique (une réaction en chaîne dangereuse au cours de laquelle la batterie surchauffe de manière incontrôlée et peut s'enflammer ou exploser).
Les fabricants adoptent des solutions de vision par ordinateur associées à l'imagerie thermique pour améliorer cette étape. Ces systèmes peuvent scanner chaque soudure en temps réel, à la recherche de défauts tels que des fissures, des lacunes ou des points faibles.
Si l'inspection visuelle permet de détecter les problèmes de surface, certains défauts sont cachés sous la surface ou provoquent une répartition inégale de la chaleur, ce que les caméras standard ou l'œil humain ne peuvent pas détecter. L'imagerie thermique peut révéler ces problèmes cachés en montrant comment la chaleur se propage dans la soudure, ce qui facilite l'identification des joints faibles ou des connexions incomplètes susceptibles d'entraîner des défaillances ultérieures.
La fabrication des batteries implique un processus précis de découpage, d'empilage, de soudage et de scellement. Chaque étape est soigneusement chronométrée et automatisée. Mais même dans des environnements contrôlés, de petits objets étrangers peuvent se glisser. Une vis desserrée ou un éclat de métal laissé à l'intérieur d'une batterie peut provoquer des courts-circuits, des dommages internes ou des incendies.
Pour résoudre ce problème, les fabricants s'appuient sur des systèmes de vision par ordinateur spécialement conçus pour la détection des corps étrangers. Ces systèmes utilisent des caméras haute résolution et la vision 3D pour scanner les plateaux et les modules avant le scellement final. Ils sont formés pour détecter les objets indésirables et réagir immédiatement, en arrêtant la ligne, en alertant un technicien ou en rejetant l'emballage concerné, sans interrompre le flux de production.
Par exemple, dans l'assemblage des batteries de véhicules électriques, la vision par ordinateur est utilisée pour inspecter les plateaux à la recherche de corps étrangers juste avant le scellement final. Ces systèmes peuvent détecter des outils mal placés, des vis desserrées ou des débris que les inspections manuelles pourraient manquer. En identifiant ces problèmes à un stade précoce, ils contribuent à prévenir les pannes électriques, à éviter les retards de production et à réduire les risques pour la sécurité.
Une fois le bloc-batterie entièrement assemblé, la dernière étape consiste à inspecter l'emballage et les étiquettes. Un joint endommagé, un boîtier bosselé ou une étiquette mal imprimée peuvent causer des problèmes en aval. Ces problèmes peuvent affecter la sécurité du produit, retarder les expéditions ou conduire à des manquements à la réglementation s'ils ne sont pas contrôlés.
À ce stade, l'inspection manuelle peut être lente et peu fiable, en particulier pour les gros volumes, alors que les systèmes de vision par ordinateur peuvent effectuer les mêmes contrôles rapidement, de manière cohérente et avec une plus grande précision.
Supposons par exemple que l'étiquette d'une batterie comporte une faute de frappe. La détection d'objets permet d'abord d'identifier la partie de l'étiquette qui contient du texte, puis la technologie OCR (reconnaissance optique de caractères) peut être utilisée pour lire et vérifier le contenu. S'il y a une faute de frappe ou une erreur de formatage, le système peut signaler l'emballage pour qu'il soit corrigé avant qu'il ne soit acheminé plus loin dans la chaîne.
Voici un bref aperçu de la manière dont la vision par ordinateur améliore la fabrication des batteries :
Bien que la vision par ordinateur présente de nombreux avantages, il y a quelques limites à prendre en compte lors de l'adoption de ces systèmes. Voici quelques facteurs à garder à l'esprit :
La vision par ordinateur modifie progressivement la fabrication des batteries. Elle permet de détecter les petits défauts, de guider avec précision les bras robotiques, d'inspecter les soudures et les joints et de vérifier l'emballage final.
Chaque étape peut être surveillée de près par Vision AI afin de s'assurer que chaque batterie répond à des normes de sécurité et de qualité élevées. Ces systèmes sont plus rapides et plus cohérents que les contrôles manuels, ce qui aide les fabricants à réduire les déchets et à éviter les erreurs coûteuses. À mesure que la technologie continue d'évoluer, il est probable que le rôle de la vision par ordinateur dans la production de batteries s'accroîtra.
Rejoignez notre communauté et explorez notre dépôt GitHub pour en savoir plus sur l'IA. Si vous souhaitez lancer votre propre projet Vision AI, consultez nos options de licence pour commencer. Vous pouvez également voir comment l 'IA dans les soins de santé et l'IA de vision dans le commerce de détail ont un impact en visitant nos pages de solutions.
Comment les piles sont-elles fabriquées et comment la vision par ordinateur peut-elle les aider ?
La production de batteries est un processus minutieux, étape par étape, qui doit être extrêmement précis. Elle commence par le revêtement de matériaux spéciaux sur de minces feuilles de métal, qui sont ensuite découpées et empilées avec d'autres couches pour former le cœur de la batterie.
Ensuite, l'électrolyte liquide est ajouté, la batterie est scellée, puis elle est chargée et testée pour s'assurer qu'elle fonctionne correctement. Enfin, elle est étiquetée et emballée, prête à alimenter toutes sortes d'appareils, des téléphones aux voitures électriques.
Les piles étant très sensibles, de minuscules défauts peuvent causer de gros problèmes. Un défaut aussi minime qu'une éraflure ou un léger défaut d'alignement peut réduire la durée de vie de la batterie, compromettre la sécurité ou entraîner une défaillance de la batterie. Étant donné que de plus en plus d'appareils et de véhicules fonctionnent avec des batteries, les fabricants cherchent des moyens innovants et plus rapides de s'assurer que chaque unité est fabriquée sans défaut.
C'est là que la vision par ordinateur entre en jeu. Les modèles de vision artificielle comme Ultralytics YOLO11, qui prennent en charge diverses tâches telles que la détection d'objets et la segmentation d'instances, peuvent être entraînés à reconnaître les composants de la batterie, à détecter les défauts de surface et à contrôler la précision de l'assemblage en temps réel.
En analysant des images provenant de caméras à haute résolution, ces modèles permettent de vérifier que chaque pièce est correctement placée et exempte de défauts. Cela permet une production de piles plus rapide et plus cohérente, avec moins d'erreurs.